Induction furnaces use different refractory materials according to the type of molten metal, slag properties, furnace capacity and operating conditions.
Induction furnaces can smelt all kinds of cast iron, such as ductile iron, vermicular graphite iron, etc. In the past, most of the melting cast iron used power frequency furnaces. Due to the advantages of high efficiency and energy saving of intermediate frequency variable frequency induction furnaces, more and more intermediate frequency or variable frequency furnaces have been used to melt cast iron in recent years.
The lining of cast iron induction furnace is generally made of quartz ramming material, and boric acid is the acid lining of sintering agent. Natural quartz has a large thermal expansion coefficient and poor thermal shock resistance due to the volume effect due to crystal transformation during use. It is not suitable for furnaces that operate intermittently.
At present, the life of this type of furnace lining is about 60 to 150 heats, and some can reach 200 heats. It is worth mentioning that in recent years, the service life of quartz linings has been significantly improved in some places, mainly using high-purity, large-grained quartz and different sintering agents.
The knotting process mainly includes:
(1) Coil knotting
Insulating glue is used to evenly coat the surface of the induction coil. The thickness of the glue layer is 8 to 15 mm. After drying, it has good insulation performance. A layer of asbestos board and a layer of glass fiber cloth are laid in the insulation layer of the coil. Layer material, and then tighten up and down with spring coils. When tamping the quartz sand, move the spring coils one by one from top to bottom until the lining is knotted;
(2) Knot the bottom of the furnace
The thickness of the furnace bottom is 280 mm, and the sand is filled in four times. The thickness of the sand filling must be strictly controlled to be no more than 100 mm per time, and the knots are manually tied for 30 minutes each time. When the knot reaches the required height, scrape it flat and place the crucible mold. It must be ensured that the crucible mold and the induction coil are concentric and tightly combined with the furnace bottom. After adjusting the peripheral gap evenly, use a wooden wedge to clamp it tightly to avoid displacement when the lining wall is knotted
(3) Knot the furnace wall
The thickness of the furnace lining is 110-120 mm, and the materials are added in batches, the thickness of the filler is not more than 60 mm/time, and the knot is manually knotted for 15 minutes until it is flush with the upper edge of the induction coil. After knotting, the crucible mold is not taken out, and it plays the role of induction heating during drying and sintering. There is also a reasonable baking and sintering process to obtain a three-layer structure (ie, a sintered layer, a transition layer, and a loose layer) lining, and do a good job of daily maintenance work to obtain a high service life of the furnace lining.
There are also fused silica knotting materials used as acid linings, especially in foreign countries. Fused silica has a small thermal expansion coefficient, and the ramming material has the characteristics of good impact resistance. At the same time, it overcomes the phenomenon that the sintered layer of natural quartz is thick or even burned through during long-term use, and retains enough unsintered layer to avoid crack penetration and ensure the safe and stable operation of the induction furnace. This ramming material is used for the lining of 50 kg-10 t induction furnaces, with a service life of 250 to 450 heats, and the service life of 20 furnace linings can reach 300 heats.
In addition, the high alumina bauxite ramming material can also be used as the lining of the molten iron induction furnace, and has better thermal shock resistance. The third-grade bauxite clinker with Al₂O₃ mass fraction of 55~66% can meet the requirements of cast iron induction furnace lining..
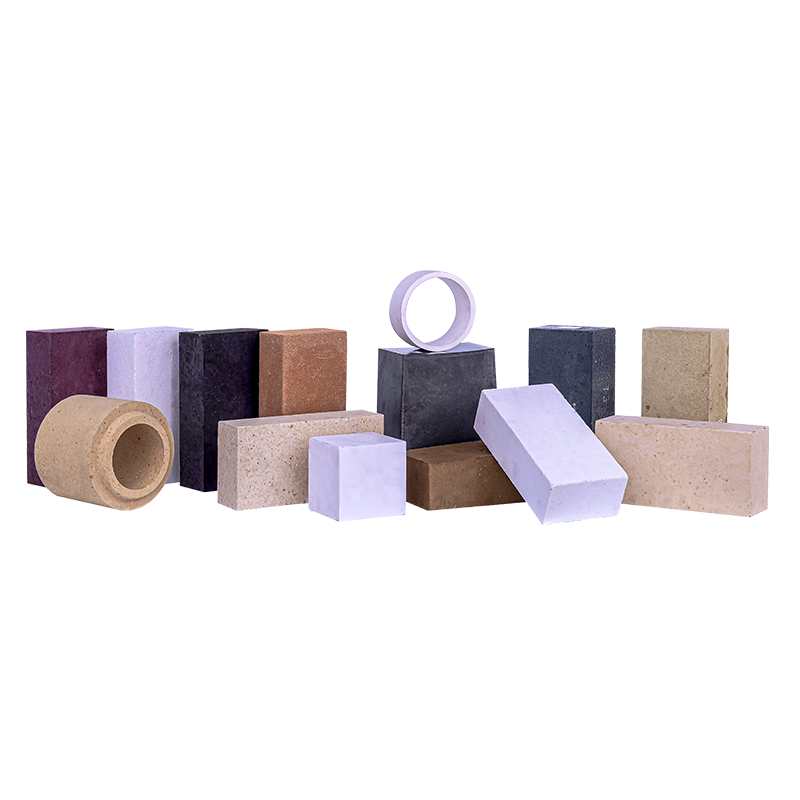