What is Temperature Rise Curve of Rotary Kiln Based on?
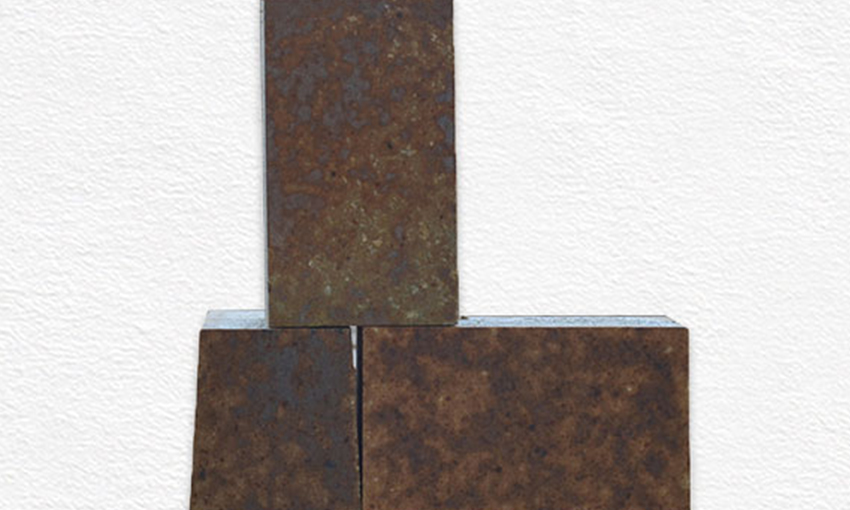
In the cement factory kiln, the temperature rise after the new refractory brick is built is very important. What is the curve based on what principle? What is the difference between the 5000t and the 2500t kiln heating curve?
The heating curve is mainly determined by the refractory material built in the rotary kiln, for example, the process of removing gravity water in the refractory at 150 ° C, the removal of crystal water at 300 ° C, and the like. The determination of the heating curve depends on the type of refractory material you use, the type of the refractory material, and the curve. The refractory material manufacturer will provide a heating curve. The 5000t and 2500t are mainly different in temperature rise time, and the heating nodes are almost the same.
Silicon Brick Heating Curve
Silica mullite brick is a refractory brick which is composed of mullite and andalusite, silicon carbide and special graded alumina as the main raw materials, which are formed by high pressure molding and high temperature firing.
Silicon Mullite Brick Production Process
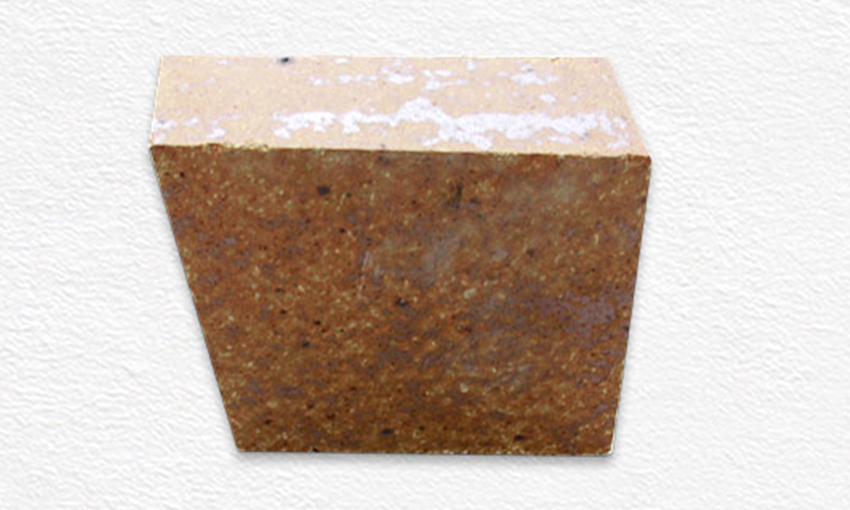
Silicon mullite brick is characterized by good high temperature resistance, wear resistance, corrosion resistance, low thermal conductivity and low energy consumption. At present, it covers the cooling zone and transition zone of most cement kilns. Silica refractory brick not only has good thermal shock resistance, but also the thermal conductivity fully satisfies the use of the cement kiln. According to the use, the temperature outside the cement kiln does not exceed 320 degrees, and the temperature detected after using the silicon brick is basically only 250. -280 degrees, greatly reducing the surface temperature of the kiln cylinder and reducing energy consumption. The heat resistance of the silica mullite brick is also very good, its load softening temperature can reach 1600 degrees, the carrier in the cement kiln is generally about 1400 degrees, there is no problem in repeated use for 1 year; and silicon mullite brick wear resistance is also very good. Fully meet the national standards for refractory materials.
Silicon Mullite Brick Application Scope
Silica refractory brick configuration is adaptable. The traditional configuration of refractory materials is usually refractory materials with different properties such as spinel fire brick, magnesia chrome brick and anti-stripping brick in the kiln mouth, the front transition zone, the rear transition zone and the decomposition zone. However, the silicon molybdenum bricks can all make these properties difficult to break and peel off, because the thermal conductivity is lower than that of the magnesia material, the cylinder is not heated too high, which not only ensures the normality of the rotary kiln cylinder. It runs and saves fuel. In addition, the use performance of silica brick is also better than that of anti-flaking high aluminum brick and phosphate high alumina brick with good wear resistance, so it can produce various grades, select by cost performance, and be used for different sections. The range of use in the kiln is constantly expanding. AZM1680 silica bricks combine high temperature resistance and wear resistance. It is very suitable for use in 4m*60m cement rotary kiln, instead of magnesium iron spinel brick, which reduces the production cost of cement enterprises. AZM1680 silica brick is soft and high in resistance to high temperature. The cover is fired into various process belts.
These performance characteristics make the silicon mulite fire brick difficult to break and peel off, and because the thermal conductivity is lower than that of the magnesium material, the cylinder is not heated too high, which not only ensures the normal operation of the rotary kiln cylinder, but also saves fuel. In addition, the use performance of silica brick is also better than that of anti-flaking high alumina brick and phosphate high alumina brick with good wear resistance, so it can produce various grades, select by cost performance, and be used for different sections. The range of use in the kiln is constantly expanding. AZM1680 silica bricks combine high temperature resistance and wear resistance. It is very suitable for use in 4m*60m cement rotary kiln, instead of magnesium iron spinel brick, which reduces the production cost of cement enterprises. AZM1680 silica brick is soft and high in resistance to high temperature.