1.The Importance of Refractory Lining Structure Design
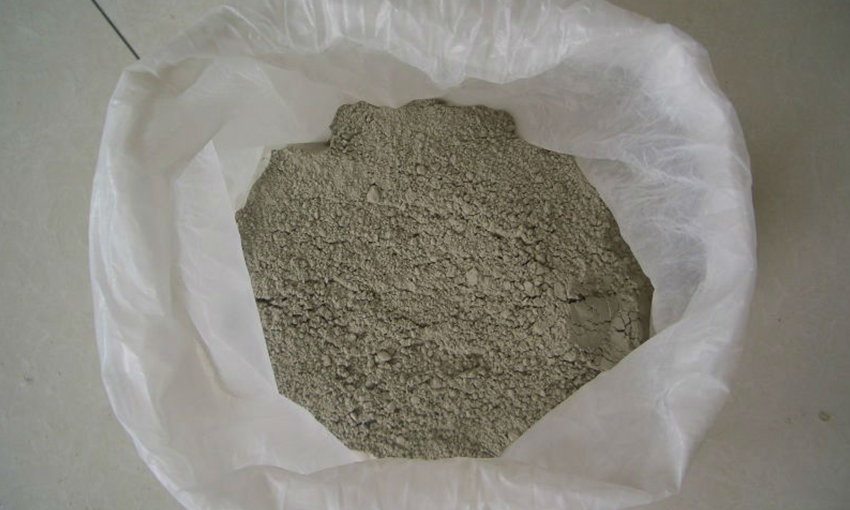
Refractory materials are the basis of high temperature application technology, the quality of the lining refractory materials plays a decisive role in whether the entire project can be put into production smoothly. Therefore, it is especially important to combine the performance of the lining refractory material with the related process. In other words, it is necessary to have a complete process and a reasonable material configuration.
2. High Performance Lining Refractory Material
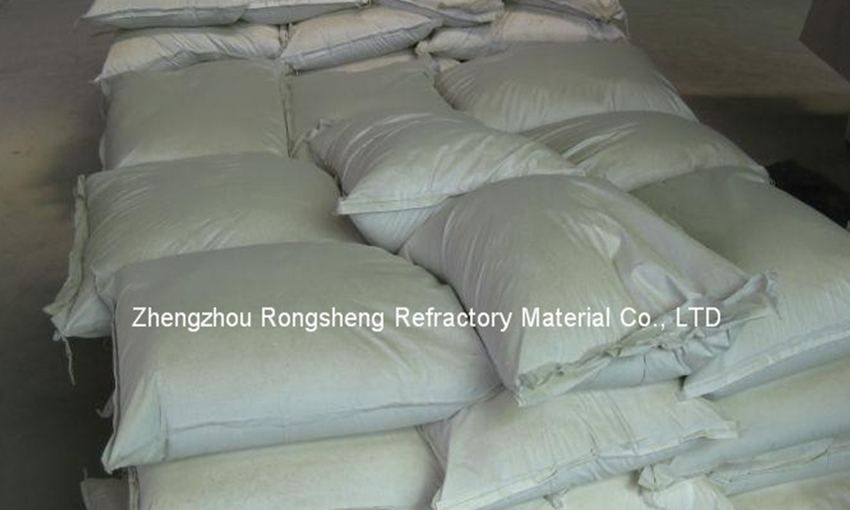
During the use of the refractory lining material, it is inevitable to suffer from changes in the ambient temperature, such as: oven, temperature rise and temperature fluctuations during operation, steam purge, on-off temperature rise and fall, etc. It is stable in operation, avoids the damage caused by the quenching and rapid heat, and improves the thermal shock stability of the refractory material, which will help to extend the service life of the lining. The lining is used in a high temperature environment, and is thermally expanded at a high temperature, and thus is subjected to extrusion to generate thermal stress. When the internal stress of the lining exceeds its own strength, peeling damage or the like is generated. In view of the particularity and severity of the working conditions, higher requirements are placed on the performance of the lining material. The current optimization of the lining performance is mainly reflected
1) Self-Flowing Castable
Self-flow castable is an emerging high-tech material that combines excellent fluidity, compactness and stability. It is called the fourth generation castable. only relying on the self-weight of the refractory material can achieve automatic flattening, degassing, compaction, and form a lining with uniform structural performance. It can be molded without vibration or a little external force to assist vibration, no noise pollution, low labor intensity, shortened work cycle, uniform structure and performance of the lining, and comparable performance of the performance of the lining and the performance of the test block. Valves, cones, which are difficult to construct. At present, GZ-16 self flowing high alumina castable has been successfully used in the three-spindle cone section of the catalytic cracking new plant. With its excellent construction performance, it has won unanimous praise from the factory and the construction party, filling the domestic gap.
2) High-Washing Parts with High Wear Resistant Lining Material
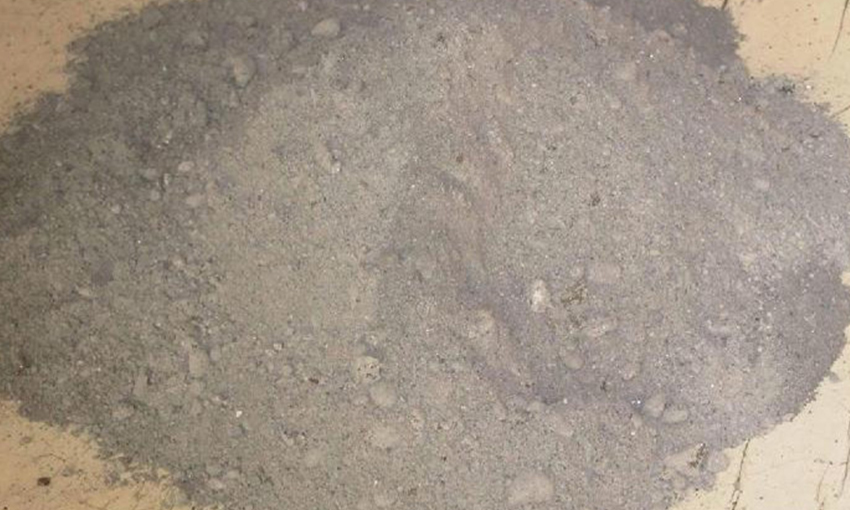
Phosphate combined with high wear-resistant lining refractory material GP-2AM (AA material) overcomes the shortcomings of traditional two-component phosphate combined with high wear-resistant lining refractory material, with short production cycle, easy to use, excellent construction performance and low temperature sensitivity. It does not bulge, the setting time is adjustable, and the physical and mechanical properties are excellent. At the same time, in accordance with the requirements of users and the use environment, the hydraulic high-wearing material GT-2AS (AB material), which replaces the phosphate combined with the high wear resistant lining, has better physical and mechanical properties and more convenient construction performance.
3) Heat-Resistant Materials for Thermal Furnaces
Without medium scouring, the operating temperature is high and the lining material is required to have good thermal insulation properties. At present, the commonly used ceramsite and expanded perlite have low refractoriness and cannot adapt to high temperature environment. We have developed a series of heat-resistant linings suitable for various temperature sections of various thermal furnaces by expanding refractory raw materials and using some high-grade synthetic raw materials. These products have the characteristics of small thermal conductivity, low line change rate and good construction performance.
4) The Catalytic Cracking Unit is Insulated and Wear Resistant Lining
Catalytic cracking is an important secondary processing method for heavy oil lightening. It is the core device of each refinery. It belongs to high temperature and high pressure devices. It has many internal parts and complex shapes. It has high speed flushing of fluidized catalyst, so it must be made of unshaped fire. The material is insulated and wear-resistant in the metal wall.
5) Low-iron Type Insulation and Wear-Resistant Lining
The carbon black deposited in the pores of the refractory causes internal stress, which is determined by the local concentration of the carbon black. This concentration is affected by the distribution and strength of the iron inclusions. In response to this kind of erosion, through the introduction of new raw materials and synthetic new raw materials, a series of low-iron heat-insulating and wear-resistant linings---LT-6C series have been developed to meet the special requirements of catalytic cracking lining design and achieved good results. And good performance. LT-6C high temperature resistant single layer lining material is made of high quality synthetic mullite clinker as aggregate, pure aluminate cement as binder, and high efficiency admixture is introduced to make bulk refractory. After the fine material and fine matching, the refractory material can achieve self-reaction, self-sintering and self-expansion, and can be directly used after molding and baking, which can save a lot of energy. The material can be applied on site with suitable liquid blending. The construction tools are few and can be arbitrarily shaped. The unique formula is used to combine the performances of ordinary refractory materials such as light weight, high temperature resistance, heat insulation, wear resistance and low iron.
6) Environmental Adaptability Technology
Environmental adaptability technology refers to the unconventional refractory material can be normally constructed under the low temperature environment and high temperature environment with poor construction conditions by introducing a composite admixture. This material technology that can adapt to various environmental temperature construction is an environmental adaptability technology. High temperature environment refers to the construction environment higher than 35 °C. Generally, the binder aluminate cement is a fast and hard substance. The high temperature environment will accelerate the progress of cement hydration and generate a large amount of hydration heat. The heat of hydration promotes the strength of cement structure. The growth of the lining refractory material quickly hardens and loses the construction performance; the low temperature environment refers to the construction environment below 10 ° C. In the low temperature environment, the cement hydration reaction slows down, and even the temperature is too low, the refractory material cannot be hardened.
7). High Quality Lining Construction, Curing and Drying
With the development of the performance of the lining refractory material, the refractory material properties are more sensitive to factors such as water addition, agitation and dispersion, and maintenance, and higher requirements are imposed on the construction technology. In addition, the maintenance and baking of the lining is very important to achieve optimum lining. When the actual equipment is baked, all the equipments are connected in series. Because the distance between the various equipments is different from the heat source, the temperature rises and the speed is different. The various parts of the equipment and the pipeline should be fully considered, and the furnace time can be extended to make the lining parts reach or Close to heat treatment requirements. From the point of view of use, the slower the temperature rise, the longer the heat preservation, and the better the moisture is baked.