
- Home
- Industry News
- Industry News
Refractory for Lining of Copper and Copper Alloy Melting Furnaces
For general copper melting furnaces, quartz, high alumina bauxite, mullite and corundum materials can meet the requirements. Due to the low cost of quartz ramming material and the convenience of furnace construction, it can be used up to 200 times in a 300-700kg furnace. Mullite or high-aluminum ramming materials or castables can be used on large-scale coreless induction furnaces used continuously, and the continuous service life can generally reach one year or more. When the working temperature is increased and the use conditions are more severe, corundum lining can be used. In recent years, large-scale coreless induction furnaces of more than 30t have appeared abroad. The 16t power-frequency copper melting furnace of Suzhou Copper Factory in my country uses corundum lining material and adds impermeability agent, which is incompatible with Mn, Ni, Al, etc. in copper liquid. The reaction occurs, no sticky slag occurs, and the service life is more than 3 years (more than 700 furnaces). Red copper is one of the copper alloys with strong permeability, with a melting point of 1083 °C. During smelting, the melt penetrates into the interior of the lining body, and oxidation occurs, accompanied by volume expansion and the formation of low-melting substances, resulting in erosion, which reduces the lining material. service life. In a 30 t copper melting induction furnace, when melting nickel aluminum bronze, the maximum temperature is 1350 ° C, and the mullite ramming material with a critical particle size of 10 mm is used, which is in good condition.
Others use pre-synthesized graphite crucibles or silicon carbide crucibles, which have the advantage of being able to be quickly replaced to save sintering time and improve the electrical efficiency of the induction furnace, so the temperature in the crucible is also high, saving energy. However, compared with the corundum ramming material, the cost is high, and the stirring effect in the crucible is reduced, which is unfavorable for the uniformity of the furnace temperature.
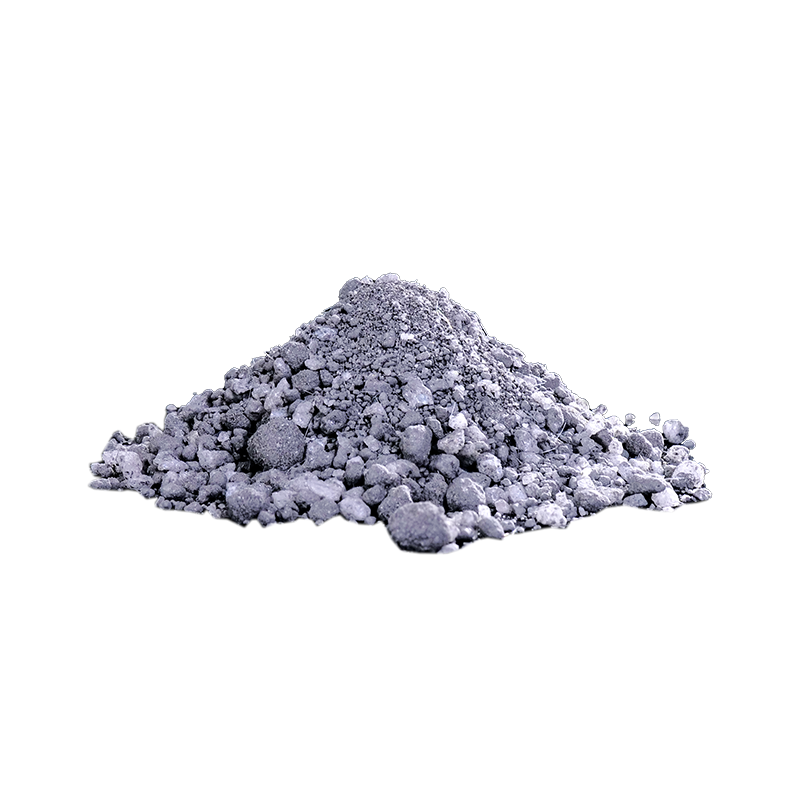