
- Home
- Industry News
- Industry News
Float Glass Kiln
Float Glass kiln Lateral, Longitudinal Annealing Temperature System Requirements.
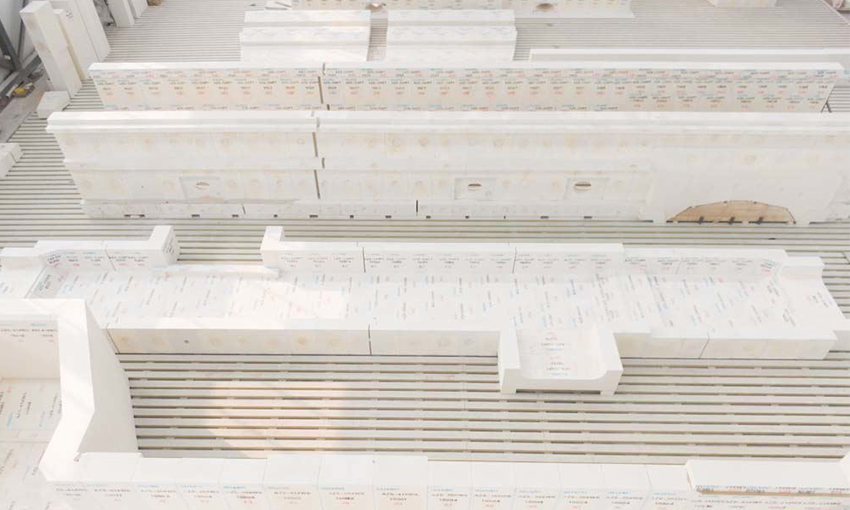
Annealing of glass is an important part of the glass production process. The purpose is to place the glass in an annealing kiln so that it is allowed to cool at a certain temperature for a sufficient period of time before the glass stress does not exceed the allowable value. To achieve this goal, a reasonable temperature regime must be determined. The temperature setting must strictly follow the morphological transformation law of the glass, and the annealing temperature should be reasonably and accurately controlled from the longitudinal, transverse and vertical directions. Otherwise, the float glass production line cannot be stably produced, and it is impossible to produce high-quality float glass.
Longitudinal Annealing Temperature System
The glass ribbon must be run at the correct temperature profile during the annealing process in order to achieve a good annealing effect. The longitudinal cooling curve is the bulk annealing curve of the glass, which is determined according to the annealing properties of the glass. The glass ribbon must be run at the correct temperature profile during the annealing process in order to achieve a good annealing effect.
The inlet temperature of the glass ribbon in the annealing kiln is established according to the temperature of the tin bath outlet. The minimum outlet temperature should not be less than 575 °C. Too low will affect the process effect of the AD zone due to insufficient heat of the glass ribbon, resulting in insufficient lateral heat solubilization capacity, or even fail to reach the control index, and supplement the heat by starting a large amount of electric heating.
The control requirements of Zone A are as follows: one must be high in heat and the other should be accurate. Two indicators require strict control in production.
The temperature control range of zone B is determined by the intrinsic properties of the glass, from the conversion properties of the plastisomer to the elastomer. The initial state of the elastomer to fully reach the elastomer determines the temperature control range of zone B. This corresponding temperature indicator, 545.3~471.3 °C, is a fixed control value. The temperature at the outlet of the tin bath determines the inlet temperature of zone A, while the inlet temperature of zone B determines the outlet temperature of zone A.
The outlet temperature of Zone B determines the inlet temperature of Zone C. The exit temperature of zone C is determined according to the annealing requirements of the thickness direction of the glass ribbon to ensure the reasonable temperature drop rate. The cooling rate should be controlled within the range of 6~8 °C/m.
The longitudinal temperature control principle of the Exit C area and the Ret area to the F area is:
1 Smooth cooling rate to prevent the generation of large temperature gradients.
2 The cooling rate of each zone must take into account the convergence of the front and rear intervals.
3 Reasonable formation of stress control effects.
The setting of the wind temperature control index in the Ret area is established based on the cooling rate of the glass body. If it is too high, the temperature gradient in the interval from the Ret zone to the F zone is too large, which is not conducive to annealing in the F zone; if it is too low, it will cause cracking due to excessive temperature gradient with the C zone. Therefore, the wind temperature in the Ret zone must be adjusted according to different pull amounts, forming thickness, and temperature conditions of the front and rear sections.
Lateral Annealing Temperature System
Before the glass ribbon enters the A zone, there must be a large lateral temperature difference. The homogenization process is a cooling system or a heating system that is controlled separately through the lateral direction of the annealing kiln. During the slow heat transfer adjustment process, the glass ribbon is brought from the original transverse section temperature. The uneven heat state is turned to the soaking state, and the temperature value corresponding to the 12th power Pa*s of the elastic starting point viscosity 10 is 545.3 °C. If this process goal is not achieved, the annealing process in Zone B will have a very adverse effect.
The lateral temperature control of Zone A and Zone B must be aimed at achieving the soaking temperature of the glass solid body. The smaller the deviation, the more favorable the elimination of permanent stress. The temperature control index is given by the adjustment of different cooling rate to achieve the annealing effect of the transverse temperature equilibrium of the glass ribbon. The measurement control temperature is different from the glass solid temperature. Due to various factors such as thickness and heat transfer conditions, the temperature difference must be correctly adjusted during the annealing and cooling process of the section. The temperature measurement control indicators are subject to the glass entity soaking target.
The lateral temperature control body of Zone C is still aimed at soaking heat, and the edge of the glass should be properly raised to increase the temperature of the edge to enable a smooth transition to the D zone. When the lateral temperature difference of the glass plate at the end of the C zone is <3~4°C, the plate surface is well cut, and the lateral temperature difference is >6~8°C, which is not easy to cut.
The lateral temperature control of the Ret zone and the F zone is based on the temporary stress control effect setting control scheme. According to the different forming thicknesses and the permanent stress states that have been formed in the A, B and C zones, the lateral temperature distribution is reasonably adjusted to achieve smooth running of the glass ribbon and to facilitate the cutting effect.
Vertical (sub-board) Temperature Control
The vertical direction (under the plate) temperature control, according to the longitudinal temperature control range, sometimes there is a certain range of deviation. It is required to be mainly on the board, and the temperature control under the board is adjusted according to the actual effect of stress formation, and it is not simply the temperature equalization as the sole control target. Whether the temperature under the plate on the A, B, and C areas is correct, mainly depends on the lateral bending of the glass ribbon. The Ret area and the F area are mainly adjusted to suit the cutting. After the glass reaches normal temperature, the difference between the upper and lower bending is equal, which indicates that the vertical uniformity of the A, B and C areas has reached the target. However, in the actual control, the temperature under the A, B, and C zone plates is slightly higher than that of the board, which is beneficial to the cutting control adjustment.
Annealing Temperature is Adjusted with Glass Thickness
When the thickness of the glass and the pulling speed change, the annealing temperature system should be adjusted accordingly to reduce the cracking and ensure the annealing quality. The thinner the glass, the smaller the temperature difference in the thickness direction, and the slower the stress generation speed; on the contrary, the glass Thicker, the greater the temperature difference in the thickness direction, the faster the stress is generated. Therefore, when annealing, the cooling rate of the thin glass can be appropriately accelerated, and the cooling rate of the thick glass can be appropriately slowed to ensure the annealing quality.
(1) The thickness is thinned, the annealing zone is appropriately shortened, and the annealing speed can be appropriately accelerated. The adjustment is as follows: the temperature in zone A is controlled according to the upper limit of the original index, the temperature in zone B is controlled according to the lower limit of the original index, and the temperature in zone C can be appropriately increased. After the thin glass is out of zone C, it is adjusted to the given value.
(2) Thin and thick, the annealing zone should be extended appropriately, and the annealing speed should be appropriately slowed down. The adjustment is as follows: the temperature in zone A is controlled according to the lower limit of the original index.
The temperature in zone B is controlled according to the upper limit of the original index, the temperature in zone C is controlled according to the upper limit of the original index, and the zone D is adjusted according to the condition of the glass plate.
Temperature System Example
The annealing temperature system of the glass ribbon determines the annealing regime of the glass, its cooling rate in the annealing zone and the cooling zone, and the production process according to the chemical composition of the glass and the permanent internal stress required after annealing and the thickness of the glass ribbon. The actual situation in the correction was made to establish a temperature regime for the glass ribbon in each zone.