
- Home
- Industry News
- Industry News
Circulating Fluidized Bed Boiler Technology
Circulating fluidized bed boiler technology is an emerging coal combustion technology in recent years. In the past 30 years, its application has developed from small boilers to supporting boilers with a capacity of 300 MW units. From a large number of practical applications, the CFB boiler has a good desulfurization function, the generation of NOx is relatively small, and it has the characteristics of good load adjustment ability, good fuel adaptability, and comprehensive application. At present, primary energy occupies the main function of the entire coal combustion, while the industry is dominated by coal power, and the quality of domestic power generation coal is crossed, so the large-scale circulating vulcanized boiler technology has strong practical significance for the development of power industry.
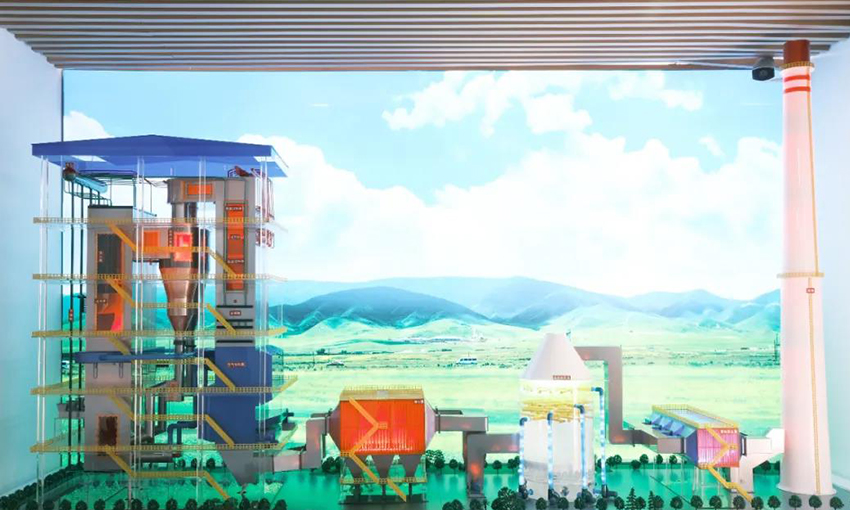
The Development Status of Circulating Fluidized Boilers
(1) Bubbling fluidized boiler technology
The fluidized bed furnace (bubbling fluidized bed) was first produced in the late 1960s. Through persistent research, the staff finally solved the difficulties. At the same time, they have been summing up experience in the exploration, which made the bubbling fluidized bed boiler technology a further step. development of. But in fact, in the product development and research of bubbling fluidized bed boilers, many people have found that the technical fuel has many limitations. In the end, they had to use oil shale as a high-ash fuel, so the technical development of bubbling fluidized bed was affected. Constraints.
(2) Small-scale circulating fluidized bed boiler technology
In the early 1980s, the National Science and Technology Commission conducted in-depth research on coal fluidized bed fuel technology for the first time, and then conducted in-depth research and development on circulating fluidized bed boilers and related products. In 1984, the 2.8 MW thermal power circulating fluidized bed combustion test in the Institute of Physics of the National Academy of Sciences was born, indicating that the fluidized bed combustion technology began to shift from cold state experiments and theoretical research to hot state. Starting in the mid-1980s, most small and medium-sized boiler manufacturers began to establish cooperative relations with the research institute, and carried out project research and development on circulating fluidized bed boilers. By the mid-1990s, more than 200 75 t/h circulating fluidized bed boilers had been put into operation. There are also many problems in the application of this type of small-capacity circulating fluidized bed boiler, which are mainly reflected in the low temperature, large wear, insufficient output, high failure rate of auxiliary equipment, insufficient automatic water level, etc., although it is currently being carried out. The optimization has also solved some problems. The application rate of the unit has been significantly improved, but the overall level of the small-capacity circulating fluidized bed boiler is still insufficient and needs to be further improved.
(2) Medium capacity circulating fluidized bed
By the mid-1990s, domestic boiler manufacturing companies had introduced a large number of advanced technologies. 220 t/h circulating fluidized bed boilers entered the domestic market. The medium-content circulating fluidized bed boilers in the units allowed domestic circulating fluidized bed boiler technology to be obtained. The overall improvement has been achieved, and at the same time it has also gained a good position in the commercial market. In this process, the most significant is the Sichuan Baima Power Generation Main Dam, which successfully put into operation a 410 t/h high temperature and high pressure circulating fluidized bed boiler, which has played a great role in the development of domestic circulating fluidized bed boilers. It not only reflects This has established a good circulating fluidized bed boiler and capacity advantages, and at the same time confirmed the impact of circulating fluidized bed boilers on domestic anthracite. By the end of the 1990s, China began to attach importance to environmental issues. At the same time, the power industry also coordinated the industrial structure. As a whole, it began to favor the transformation of old units to promote the application of circulating fluidized bed boiler technology. Here comes a new bright spot. In 2009, Xi'an Thermal Power Research Institute and Harbin Boiler Factory conducted research on 330 MW CFB boiler, and Jiangxi Branch Company officially started operation after trial operation.
2.Technical characteristics and existing problems of circulating fluidized bed boiler
The technologies of pressurized circulation, integrated coal gasification, and atmospheric circulating fluidized bed are internationally recognized clean coal technologies. Atmospheric circulating fluidized bed technology has always been an internationally recognized commercial technology. This technology is a new type of clean and combustion technology that emerged in the 1980s. It can handle low-quality coal and high-sulfur coal well and meet international development requirements. From the point of view of the coal cleaning technology of the circulating fluidized bed, it has great advantages, such as: good adaptability, rather than being limited to various high-ash fuels of oil shale, with a large adjustment range and meeting environmental protection indicators. Due to the influence of factors such as the low-temperature combustion characteristics of circulating fluidized bed boilers, the concentrations of nitrogen oxides and sulfur dioxide are relatively small, the oxide generation temperature is generally around 1000 ℃, and the emission concentration (mass fraction) is controlled within 200×10-6. It is also difficult to achieve with pulverized coal and chain furnace, because the cyclic combustion makes the cinder without any carbon material and appears as small yellow-brown particles, so it can be used as a cement admixture to reduce the total slag output.
Judging from the current domestic circulating fluidized bed boiler problems, they are mainly manifested in high-temperature separators, design values, coking of material returners, wear of heating surfaces and refractory materials, and boiler exhaust temperature.
In view of the problem of poor fluidization, it is necessary to ensure that the small holes in the air distribution plate are unobstructed, and at the same time, clean the bed surface and the small holes of the hood. After operation, the air volume must be greater than the critical fluidized air volume. During the pressure increase and temperature rise period, it is necessary to avoid clogging of the hood inside the furnace, and at the same time control the coal particle size between 6-10 mm, so as to avoid adverse effects on the safe operation of the boiler. By controlling the content of coal-burning iron nuggets, and regularly removing large particles, so as to have a good fluidization. When adjusting the load, the wind cannot be increased or decreased sharply. For over-temperature coking, the bed pressure must be controlled first to avoid direct contact between the coal and the hood. When starting the ignition, it is necessary to reasonably control the fuel gun and the air distribution so that the fuel can be completely burned, thereby avoiding unnecessary coking.
The development prospects of circulating fluidized bed boiler technology
Circulating fluidized bed boiler technology has become a typical commercialized clean coal technology. While the global coal storage continues to decrease, it also puts forward many new requirements for environmental protection.
As an important energy source, coal reserves will be reduced if it is used in large quantities, and the large-scale pulverized coal boiler industry will be restricted. In fact, the circulating fluidized bed has good adaptability, is suitable for different fuel combustion, and at the same time helps the city to deal with garbage, so it will get government support, which is also the advantage of circulating fluidized bed boiler technology.
4. The circulating vulcanization boiler has the functions of low-temperature combustion and air classification. It can help generate oxides. Compared with the boilers of the same period, it can reduce the nitrogen and oxygen content, so that the mass concentration of NO is always within 300 mg/m3. Deep denitration and desulfurization has become a key research direction. CFB is widely distributed in China. Although there are many in number, the technology needs to be further improved to make deep desulfurization a development goal. Circulating fluidized bed boilers have many technical advantages for high-sulfur equipment and high-ash equipment that are easily combustible. For low-load peak-shaving power plants, circulating fluidized bed boilers have many advantages for combustion. At present, 410 t/h and 220 t/h circulating fluidized bed boilers have been put into operation. In the entire development, the technology will be progressively larger, so the circulating fluidized boiler has good vitality and application prospects.
5. Conclusion
The heat of the circulating fluidized bed boiler is mainly realized by the circulation of high-speed, high-concentration, and high-flux solid materials. The transfer and exchange of heat, mass and momentum in the furnace are very rapid, making the temperature distribution in the entire furnace very uniform, so It has the advantages of low emissions and good adaptability. Various circulating fluidized bed boiler technologies are being updated and improved. At the same time, the pressurized circulating fluidized bed combustion technology is also under research and development. The combined steam power generation and pressurized bed gas greatly improve the thermal efficiency, so the cycle Fluidized bed combustion technology will usher in innovation. The application of fluid circulation combustion to enterprises can not only improve work efficiency, simplify work process, but also improve work efficiency.