At present, intermediate frequency furnaces below 500kg are mostly used for melting cast steel and special steel. The inner refractory materials include dry ramming materials such as quartz (occasionally used), magnesia, and magnesia spinel, with a service life of 50~ 150 heats. Magnesium ramming material is a refractory lining with fused magnesia as the main raw material. It has high refractoriness, excellent corrosion resistance, and is especially stable to alkaline solution and slag. However, it has a large thermal expansion coefficient and a high sintering temperature. During the use process, due to expansion and contraction, the lining will crack and peel off. Therefore, it is more suitable for furnaces with magnesia ramming materials below 500 kg. The magnesia spinel ramming material is made of magnesia as the main raw material, and an appropriate amount of spinel is added. Because its thermal expansion coefficient is smaller than that of magnesia, and the secondary spinelization in use causes the material to expand, it can inhibit the The generation and development of cracks, and the excellent slag resistance of spinel, can be used for the lining of induction melting furnaces of about 1 t.
At present, the number of melting and holding furnaces with a capacity of more than 1 t is gradually increasing, and the development of multi-variety melting, high-temperature melting and high-power rapid melting makes the use conditions of the induction furnace lining extremely harsh. Therefore, the melting of large cast steel and special steel puts forward higher requirements on the performance of the refractory lining of the induction furnace. Therefore, it is required that the refractory lining of the special steel melting furnace for cast steel must have excellent high temperature performance, that is, corrosion resistance, no cracks on the heating surface contacting molten steel, no leakage of molten steel and other problems. In order to meet these requirements, fused white corundum or dense corundum is generally selected, and an appropriate amount of magnesia or aluminum-magnesium spinel is added, and this corundum-spinel ramming material is popularized and applied in large-scale molten steel induction furnaces. Fused corundum has the advantages of good fire resistance and strong corrosion resistance. Compared with periclase or spinel, corundum has the advantages of small thermal expansion coefficient and good thermal volume stability. At the same time, it produces secondary spinelization during use. The volume expansion can effectively inhibit the generation of lining cracks. Therefore, by using the aluminum spinel ramming material lining, the hot surface cracking of the lining is controlled, and the microcracks are significantly reduced. The service life of this material on a 3t~5t induction furnace is 200~400 heats.
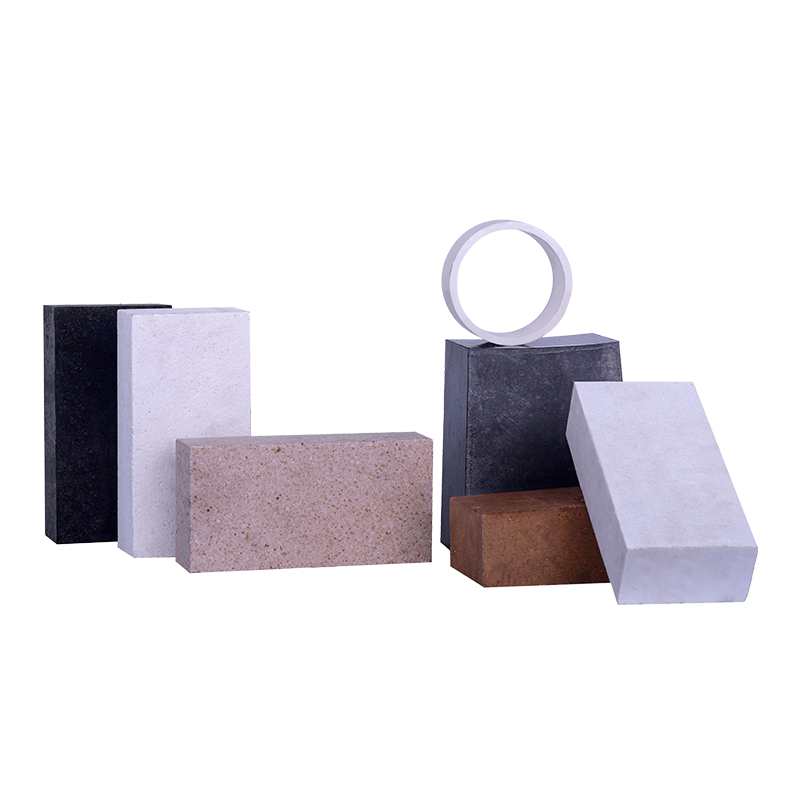